Industries
Machine vision camera: ensuring precision and reliability in industrial applications
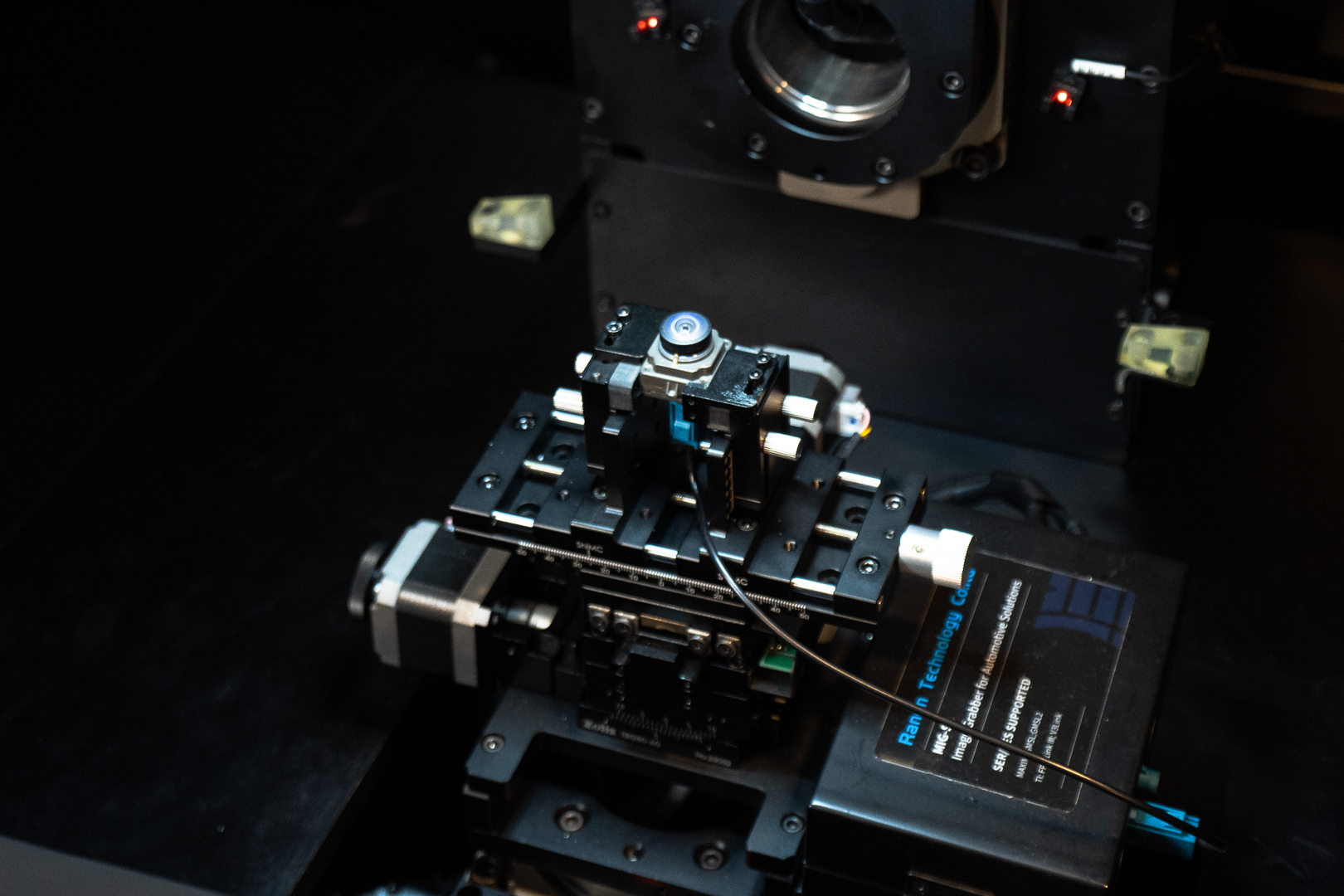
Machine vision cameras can be set up in production lines or mounted on moving parts such as robot arms in order to acquire images in industrial settings for such purposes as checking manufacturing tolerances, localization and geometrical measurement of objects, remote monitoring, etc. Such cameras can be integrated into an environment with external lighting or provide their own light source, and may cover different spectral bandwidths (RGB, IR, UV, etc) and sensitivities to light.
They are typically expected to be powered on and available at all times for extended timespans measured in years, sometimes in difficult conditions (extreme heat or cold, vibrations, etc). Controlling the image quality of the camera system is critical to guaranteeing accuracy and repeatability of the installation, as well as to quickly identifying failure modes over time and thus avoiding productivity losses. Analyzer’s flexible testing charts come in different sizes, from close-range inspection charts that can be integrated inside an inspection line to large-scale charts mounted on walls or on easy-to-move wheeled easels.
The positioning markers on such charts facilitate obtaining automated measurements of sharpness, noise, color rendering, geometrical distortion, and frame rate (among many other metrics) in any condition. The Analyzer measurement software suite provides plenty of options for evaluating precise image quality metrics at any resolution, and in both still image and video formats.
By integrating our Python API into your systems or even by building custom testing solutions with our unitary measurement tools, you can test your existing cameras with easy-to-use measurement reports and documented numerical guidelines; evaluate, check and compare specifications for off-the-shelf camera systems with standards-compliant measurements; and automatically receive alerts whenever image quality parameters deviate from their nominal values.
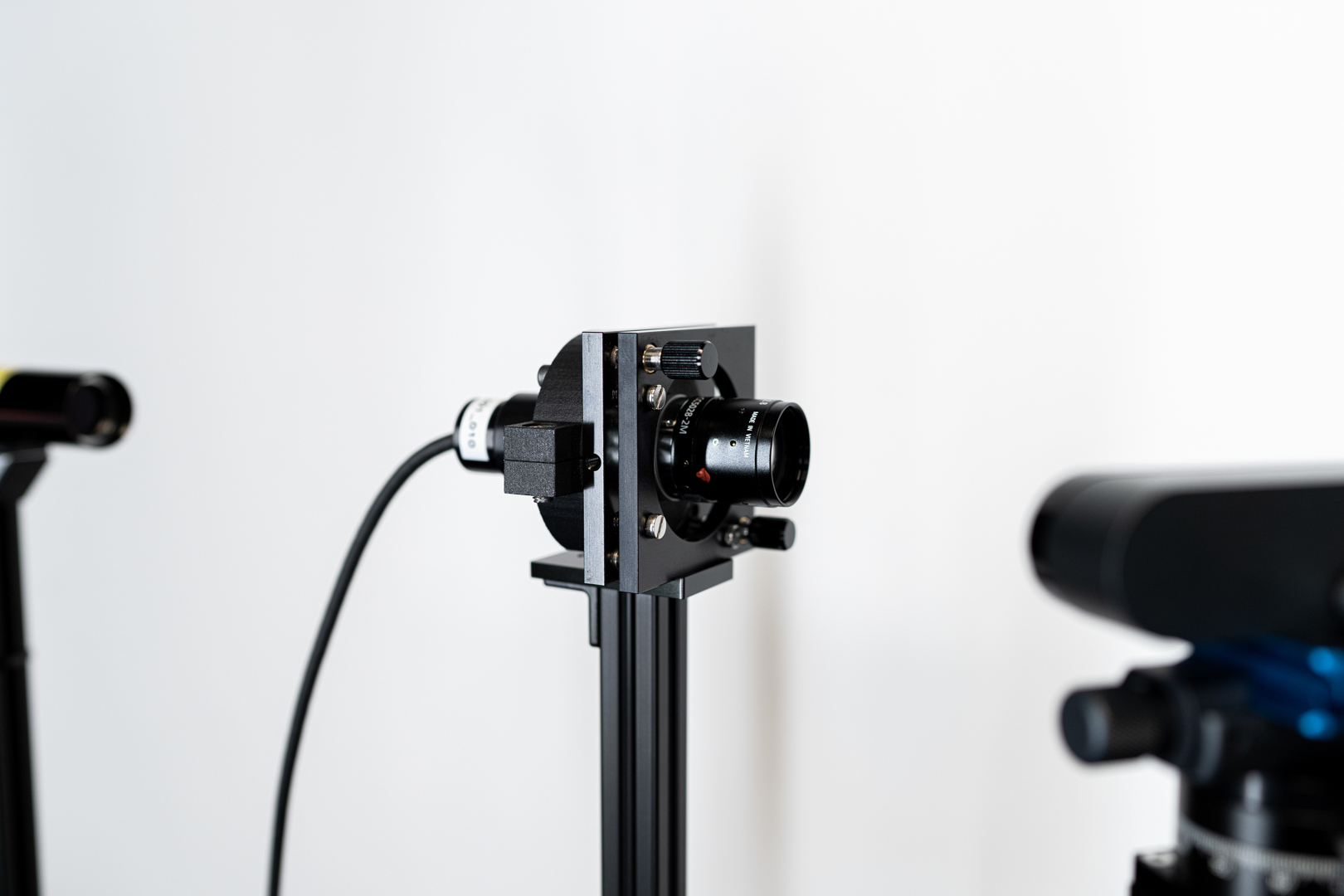
Engineering Services
DXOMARK puts its 20+ years of expertise at the service of its customers to provide an impartial measurement report, as thorough as necessary, on the sensors available on the market. Our methodology ensures the accuracy and repeatability of results, enabling them to be compared throughout the Camera Analyzer laboratory installed worldwide. Our decades of expertise enable us not only to offer a solid base of standard tests but also to develop state-of-the-art test tools and the challenges & needs of each customer.
These tests feed data into the camera industry, publicly on DSLRs, Smartphones, and now Laptops. However, our expertise extends far beyond the publicly visible part, with various camera testing in particular. DXOMARK remains the leader in camera testing, and our reports can be used as a selling point, too, by comparing competing systems with the same measurements.
The next challenge is to build an analysis of these results to establish a choice. Having already tested several hundred cameras in the Automotive sector and several thousand across all industries, security, AR/VR, etc. DXOMARK can provide a detailed analysis of the results provided in a test report, as well as the targets to be reached according to the applications targeted.
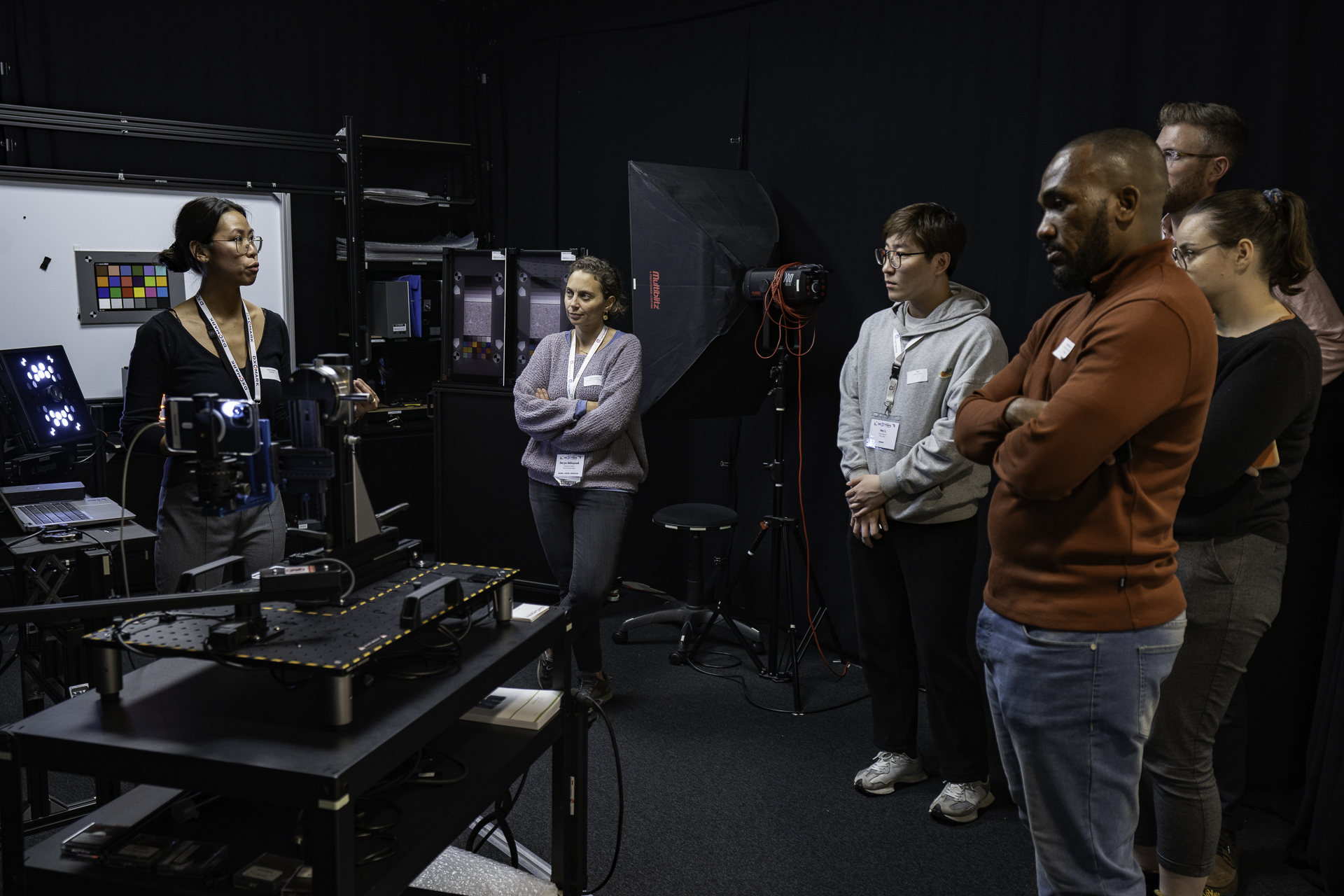